Product
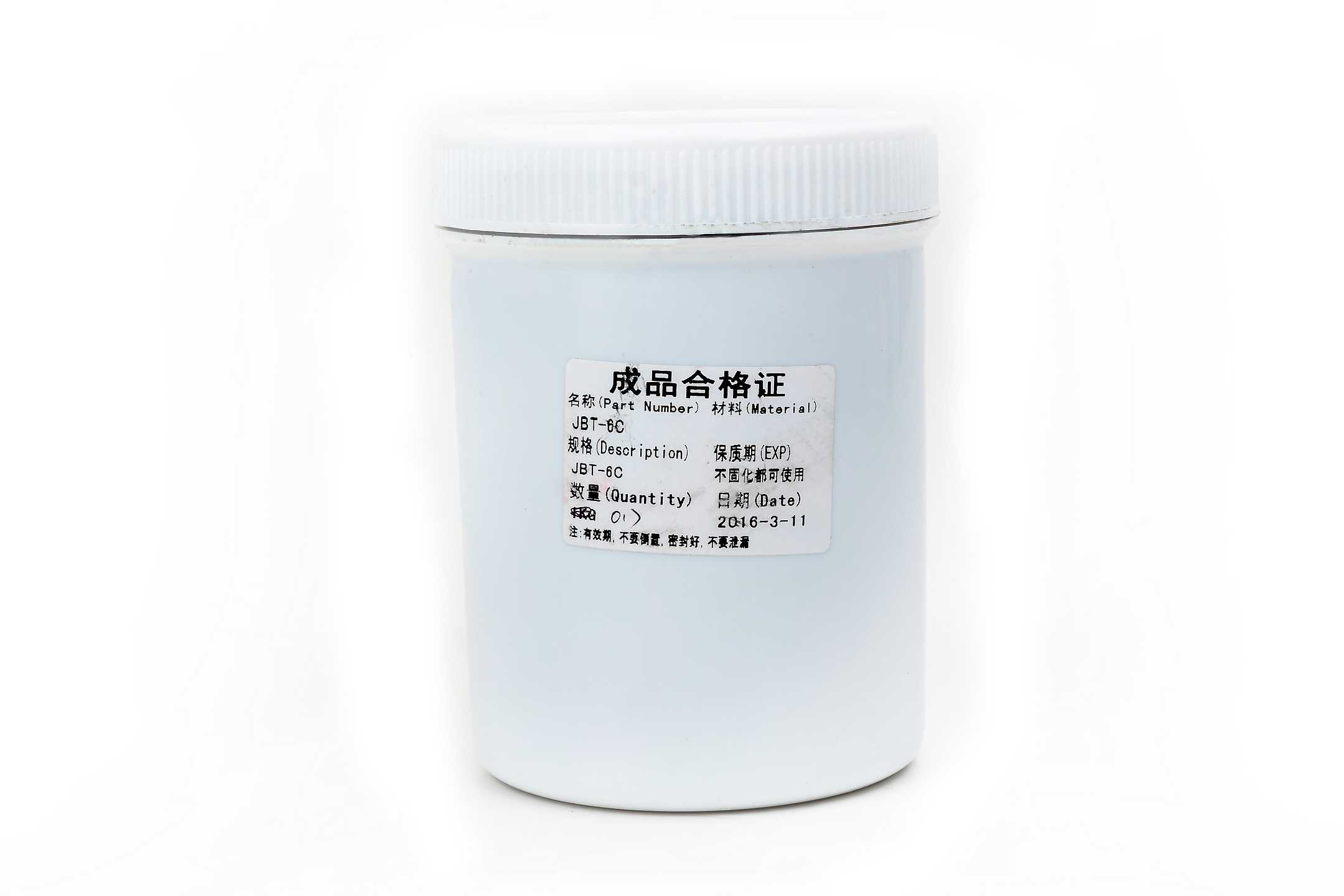
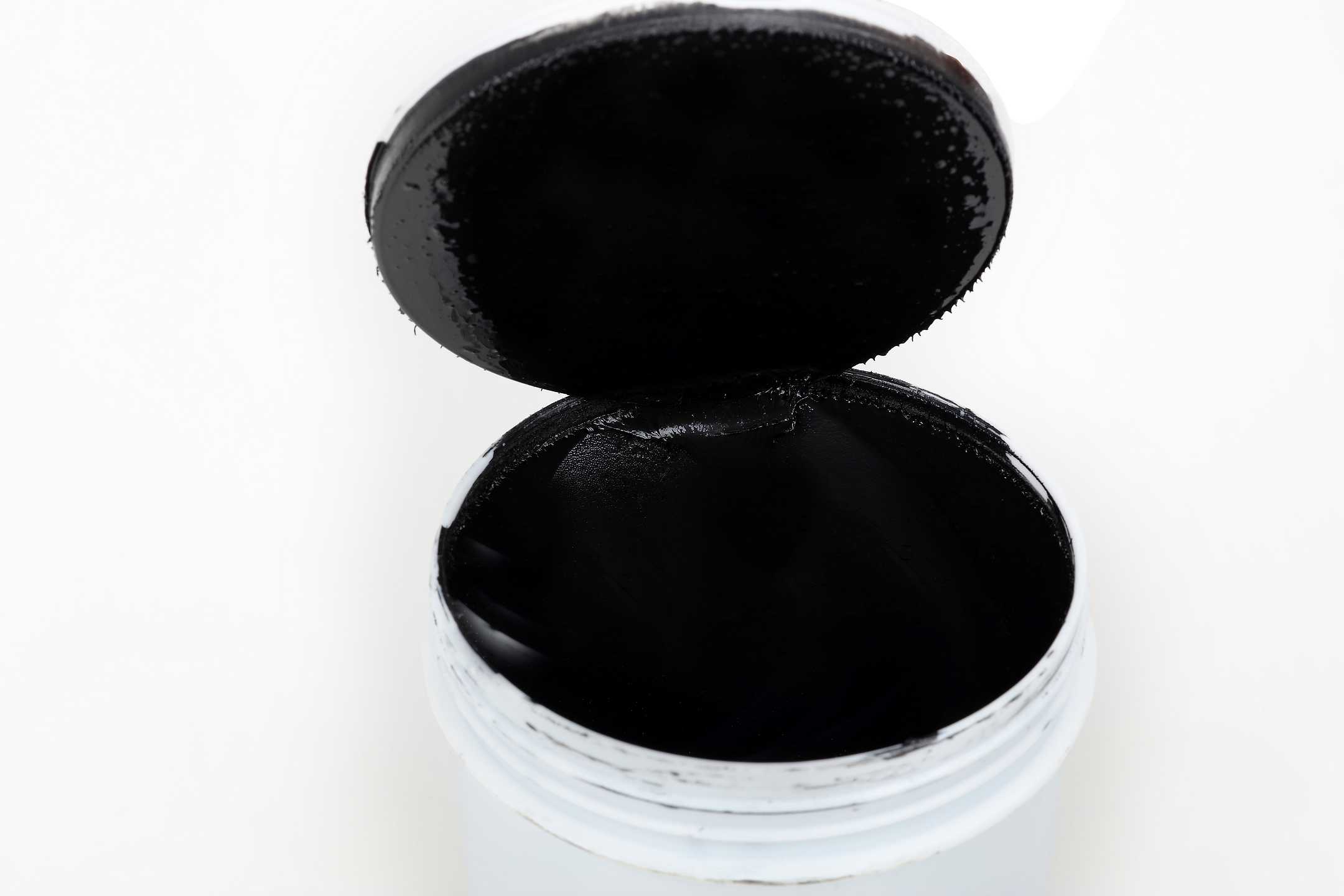
JBT
PROPERTIES & CHARATERISTICS
Epoxy anti-wear coating slydway material(anti-wear coating for short) is a kind of replication material that contains modified epoxy matrix, varies kind of lubricating material, reinforced material and other additives. Its main properties are as follows:
After years of proving, slydway with JBT anti-wear coating has many uncomparable advantages in processing and tribological properties. JBT is widely used in manufacuring and maintening machine tools:
- easy processing, replicated moulding, high accuracy, high surface quality, no need of artificial scraping, save manpower and time, lower production and maintenance costs.
- paste-like beofore curing, excellent processing properties, wide application range, convenient to process friction pair and static guide rail with high excuracy and complicated surface shapes, convenient to repair wear dimensions and blowhole and pull of the metal surface.
- low friction and no stick-slip behavior
- excellent anti-abrasion performance even in the event of failed lubrication, since the coating material’s self lubricating effect, it can avoid burining of the mating friction surface.
APPLICATION RANGE
JBT anti-wear coating mainly applied to manufacturing friction pair such as guideways, sleeves and compensating mating dimensions. Its advantages is more apparent in some large guideways with complicated surface shapes. Its main applications are as follows:
APPLICATION METHOD
Coating Slydway Design
In a friction pair, we generally choose the smaller one for coating, and another one for replication. The coating surface be machined to the zigzag shape as shown in Table 2. Coating thickness generally be 1~3mm. Oil groove depth thicker than the coating for about 0.5~1mm. Coating shoud be higher than the support side for 0.3~0.5mm, as Table 3 show.
According to the shape of the slydway, coating slydway can be flat slyway, v-shape slydway, circular slydway(e.g. vertical lathe slydway), curved surface slydway, screw-nut strips, gibs, etc, as picture 3 show.
Picture 4 Design for Anti-wear Slydway
Coating Dosage & Hardener Adding Amount
JBT coating should be used together with HNG hardener, which is specially prepared for the aboved two coatings.
Calculating Formula for Coating Dosage: WT=K·A·δ·d(g)
Calculating Formula for Hardener Adding Amount: WG=P·WT/100(g)
A——coating area(cm2); WG=P·WT/100(g)
d——coating specific gravity(g/cm3) δ——coating thickness(cm);
P——hardener adding amount for 100g coating(g) K——spare coefficient(表3)
Table 3
Release Agent
When the coating area is small, we can use a commercially available 1501 or 295 silicone grease. Coating the grease on the replication surface with a clean cloth. When the coating area is arge, add some PMMA fragments to the aceton solvent according to the weight ration of 0.5~1%,brushing it to the replication surface. Pay great attention to back and forth brushing is not allowed.
Positioning Adjustment
Flexible appliction according to different objects and precision requirement. Use aided positioning tools when precision requirememt is high, as picture 5 and 8. If not, apply simple positioning method. When maintening closed planer worktable, as picture 6 show, positioning with some copper bars on the support sides using 501 or 502 fast adhesive.
Picture 5 Positioning with Aided Tools Picture 6 Positioning with Small Copper Bars
Coating Slydway Processing Method
a. Scraping
- machining coating surface as picture 7, washing it with gasoline or metal solvent, and again with aceton
- washing replication surface and coating with release agent
- adding hardener and stirring coating(can be processing on the drilling machine, agitator machined to a propeller shape)
- coating homogeneously on the coating surface, scraping the cross section to an arc shape
- pressing the coating surface onto the replication surface, demould after 24 hours curing time
Picture 7 Arc Scraper and JBT Coating Arc Cross Section
b. Injection Method
- machining the coating surface to a zigzag shape.
- cleaning the replication surface and coating it with release agent. Replication surface can be on another processing axis or on the original.Adhesive a tinfoil or maylor with 501 or 502 adhesive.
- pisitioning adjustment according to the concrete condition.
- adding hardener and stirring the coating, then put into the injecto, be sure that without any air.
- injecting coatings, demould after cure. Put into use after neccesary cleaning and refitting. Picture 8 shows the injection method of a lathe tailstock.
Picture 8 JBT Coating Compensating to the Lathe Tailstock
PRECATIONS
- coating slydway after moulding can be machined with hand saw, hand grinding wheel, abrasive paper and scraping knife. Directly hammering on the coating surface is strictly forbidden.
- coating slydway should be processed at a temperature above 15℃.
- cleaness of the coating surface directly effects the bonding strength, removal of oil and stains and rust should be strictly carried out.
- expcept the coating surface(and places with oil stains), release agent should be applied where the coating will flow to.
- using time means the time when adding and stirring the hardener to the time the coating loss flowability, approximatily 1~2 hours. Using time is shorter when the temperature is higher. Pressing should be finished during this period.
- storage of coating and hardener should avoid sunlight. If there is layer phenomenon, stirring it before usage. Coating storage life is one year. Replication moulding is in a friction pair, with a surface(replication surface) as the base and coated with release agent. And then another surface(coating surface) coated with coating and withhold onto the replication surface to replicate a surface consistent with the base.